Cold Joint Ices Building
December 22, 2020
Urethane Crack Injection Ends Years of Pain
PROBLEM
Imagine this: Every winter, you get massive ice dams down the side of your west-facing commercial building. The ice is so bad, it sometimes rips the through-the-wall intake & exhaust furnace vent pipe off. The ice pours down, in slow motion, along 100 feet. This goes on for 20 years, until one day, you call a crack injection specialist who solves the problem.
BUILDING HISTORY
The building, used for manufacturing, is a re-purposed cold war ATT site. Built in the cold war to provide power boost to land-line phone signals in case of a nuclear attack, it was designed to withstand a nuclear blast and lock up in response to gamma rays before the blast wave could enter the building. This was when signals were carried on copper, before cell towers and microwave signals. There are some 200 of these around the country. Everything was below grade, except for a small cover over the original stairway entrance. The walls are 18" thick concrete, and the roof is made from concrete in a hip-roof style. That roof is buried under ground & on top of it rests a solar field. The current owner bought it over 20 years ago, dug out one side for an entrance, a shipping bay and some windows on the main floor.
On the west side of the building, the earth on top was originally held up by a plywood wall and fence. This was replaced by a concrete wall about 5' tall, set back 3" from the outer edge. The 100 foot horizontal cold joint between the new retaining wall and the side of the building leaked year round, due to the slope of the hip roof. And produced the massive ice dams in the winter as the afternoon sun melted the ice and then it re-froze as the sun went behind the trees.
THE FIX
The owner retained us to stop the water. We came to an agreement, with the owner providing a man-lift. We spent 3 days opening, porting, patching and injecting the joint with CME Foam Injection Urethane. There were many spots where the ports just slipped into the cold joint, and others we had to open up. The agreement includes coming back in the spring for up to 1 day for additional injection if needed. At this point, it looks like there are 2 small spots where a bit of water leaks through.
FEEDBACK
Here are a few of his comments since we injected the leaky joint in October:
December 9: "We’re getting into the ice season when we’d begin to see ice building up on the wall. Glad to say no sign of any yet. Small damp spot or two but very minor I’d say. I’m feeling pretty good about results. You should too. Nice work."
December 21: "Happy to report your work on the wall has been a complete success. Not a hint of ice unlike past years. Very nice job gentlemen."
Imagine this: Every winter, you get massive ice dams down the side of your west-facing commercial building. The ice is so bad, it sometimes rips the through-the-wall intake & exhaust furnace vent pipe off. The ice pours down, in slow motion, along 100 feet. This goes on for 20 years, until one day, you call a crack injection specialist who solves the problem.
BUILDING HISTORY
The building, used for manufacturing, is a re-purposed cold war ATT site. Built in the cold war to provide power boost to land-line phone signals in case of a nuclear attack, it was designed to withstand a nuclear blast and lock up in response to gamma rays before the blast wave could enter the building. This was when signals were carried on copper, before cell towers and microwave signals. There are some 200 of these around the country. Everything was below grade, except for a small cover over the original stairway entrance. The walls are 18" thick concrete, and the roof is made from concrete in a hip-roof style. That roof is buried under ground & on top of it rests a solar field. The current owner bought it over 20 years ago, dug out one side for an entrance, a shipping bay and some windows on the main floor.
On the west side of the building, the earth on top was originally held up by a plywood wall and fence. This was replaced by a concrete wall about 5' tall, set back 3" from the outer edge. The 100 foot horizontal cold joint between the new retaining wall and the side of the building leaked year round, due to the slope of the hip roof. And produced the massive ice dams in the winter as the afternoon sun melted the ice and then it re-froze as the sun went behind the trees.
THE FIX
The owner retained us to stop the water. We came to an agreement, with the owner providing a man-lift. We spent 3 days opening, porting, patching and injecting the joint with CME Foam Injection Urethane. There were many spots where the ports just slipped into the cold joint, and others we had to open up. The agreement includes coming back in the spring for up to 1 day for additional injection if needed. At this point, it looks like there are 2 small spots where a bit of water leaks through.
FEEDBACK
Here are a few of his comments since we injected the leaky joint in October:
December 9: "We’re getting into the ice season when we’d begin to see ice building up on the wall. Glad to say no sign of any yet. Small damp spot or two but very minor I’d say. I’m feeling pretty good about results. You should too. Nice work."
December 21: "Happy to report your work on the wall has been a complete success. Not a hint of ice unlike past years. Very nice job gentlemen."
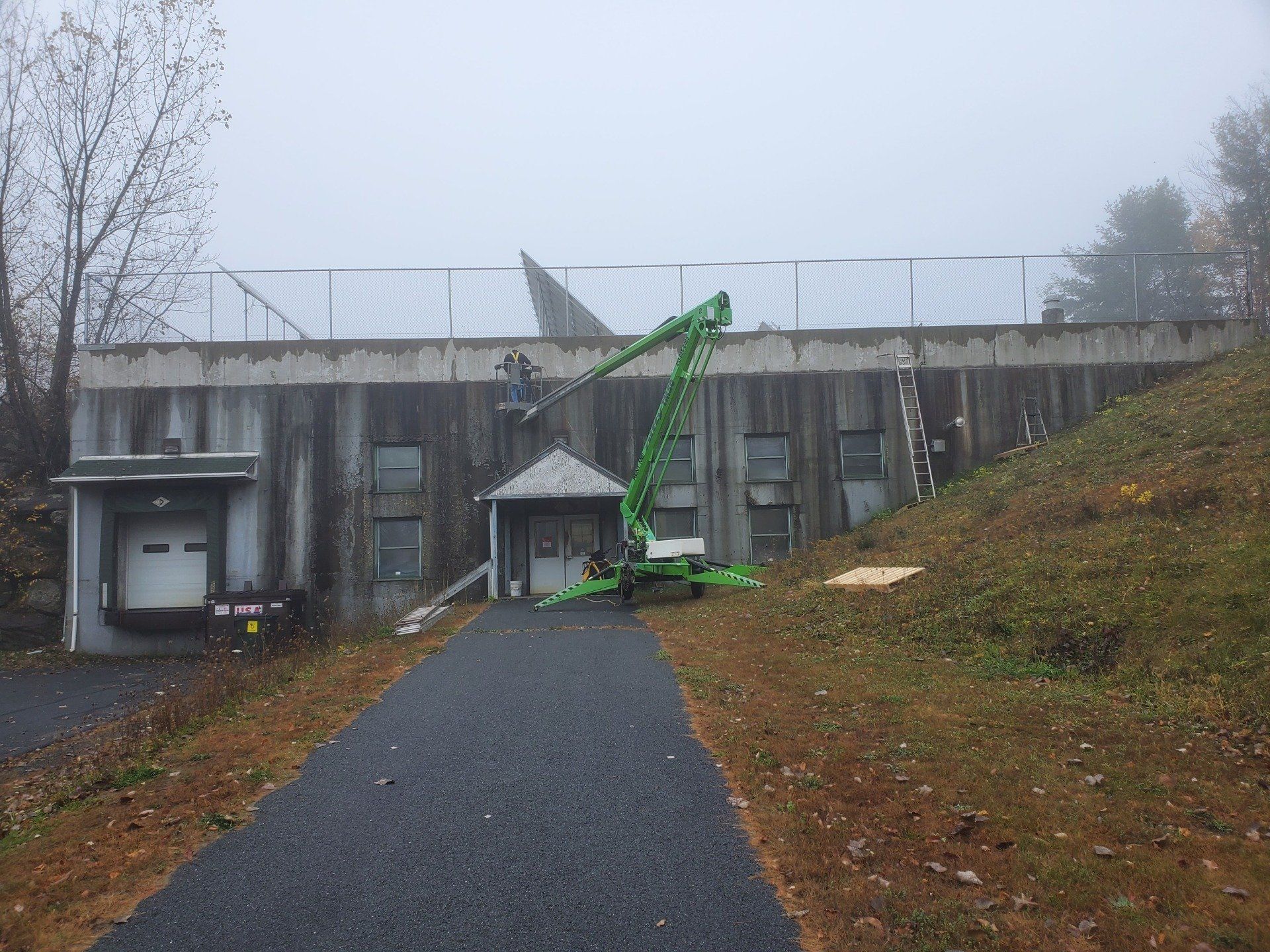
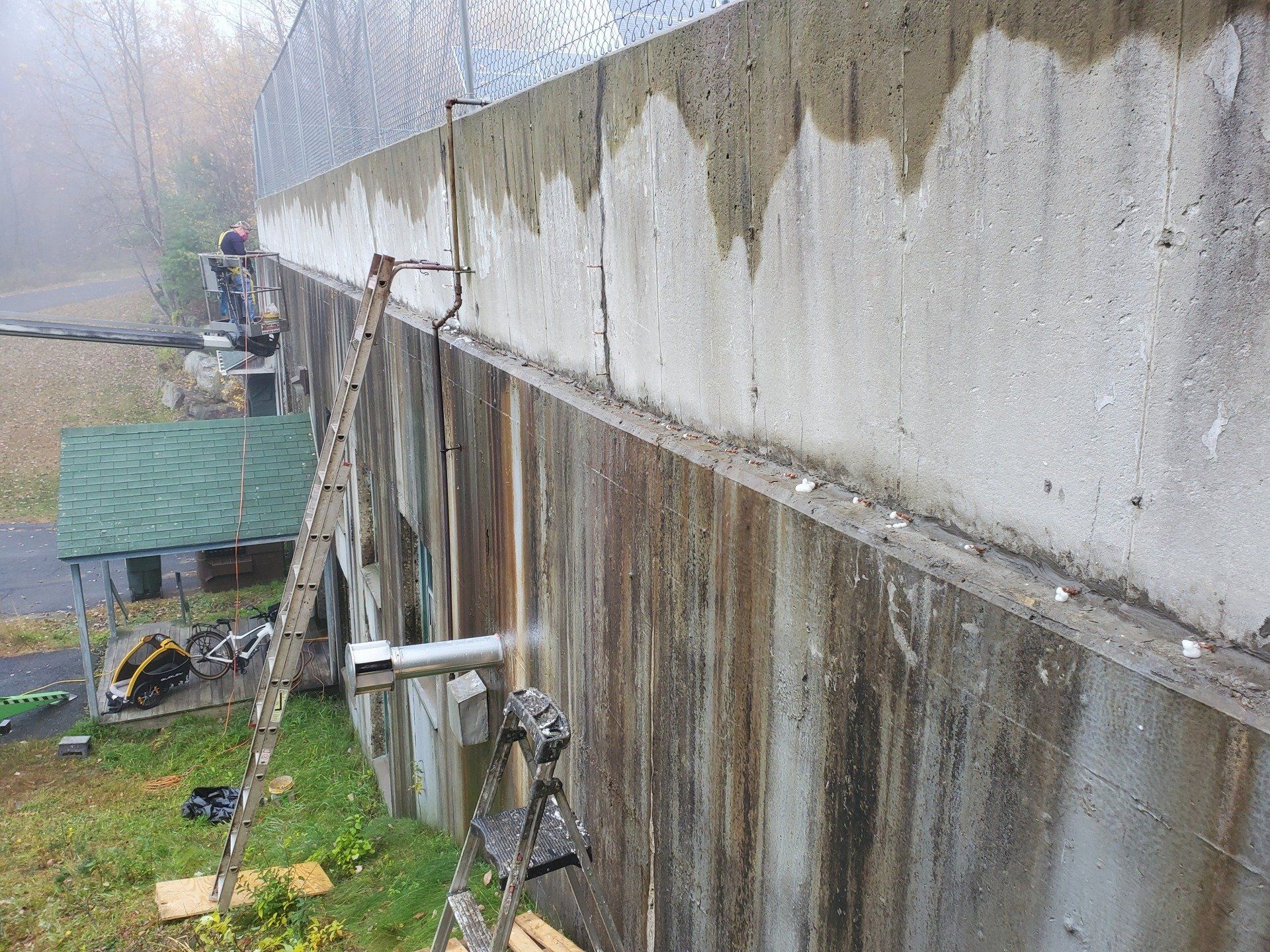
Covid-19 Practices
I injected a half-height stub wall today with a serious leak, on the far edge of my service territory. The water came in the back of the laundry room, spreading under the framed wall and into the under-house garage. They had a local handyman give them a quote and he described the job as Vee-ing the crack out and then filling it with hydraulic cement. When the price he quoted seemed too high, with no guarantee of success, much less permanence, they looked further and found me. I explained that I inject the crack completely with urethane resin, and that it comes with a life time guarantee. That is a good foundation repair. So why did they pick me over the local guy? THE COST WAS THE SAME! The local handyman wanted the same price for the job that was only a surface patch, with no guarantee, as I was offering WITH a guarantee. Now I'm not saying I'm going to match every handyman's price on a foundation repair. What I am saying is that you can get the job done right, and it is well worth it!
Share On: